内燃机首创技术一缸孔表面的热喷涂涂层
在铝制汽车缸体里,使用铸铁或冷作硬化铸铁做衬套是目前的最先进的工艺技术。为了能够制造更薄内壁和更轻重的铝合金发动机,这种衬套会被热喷涂铁基涂层所替代。这些喷涂层更薄,活塞和缸孔表面的摩擦也减少了。
发动机制造上的这项新技术,为确保最佳涂层附着度,需要在喷涂之前用使用特制工艺保证缸体表面质最。应用玛帕刀具方案,为了让喷涂的涂层能最好地与缸孔表面互锁、附着,用PCD刀片来加工缸孔表面的特定结构。涂层后,再用6刃PcBN刀片的精加工刀具精加工。这样,缸孔表面的几何形状就为最后的精珩做好了准备。精加工刀具配有冷却液驱动装置和切削补偿,以增加刀具寿命。
加工高强度钢涡轮增压器的完整加工方案
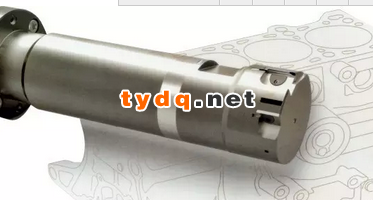
减小尺寸和涡轮增压是推动现代发动机发展的驱动力。过去,加工中心和车床用于生产涡轮增压机的涡轮和压缩机壳体。复杂的几何形状加工,尤其是涡轮壳体加工,因使用高强度和高耐热性的铸钢而更加麻烦。在-40℃到1050 ℃的温度变化范围内,这些材料的微观结构并不发生改变,这就使刀片上的载荷变得相当的高。
现代生产方式能实现在一部机床上完整加工。使用机电一体式刀具系统以及插补车完成轮廓和凹槽。整套加工刀具还包括许多加工步骤。立装刀片技术紧紧地将刀片固定在刀体上。除了稳定性外,立装刀片技术可以使用大前角刀片,这大大有利于高强度钢的加工。
可靠、经济性的加工缸盖上的烧结材料
最近几年,尺寸减小也改变了缸盖上的气门结构。气门座圈和气门导管的尺寸也逐渐的一代一代减小。与力求发动机尺寸更小,性能更好的原则相一致,用于气门座圈的材料需要经得起大载荷与高温。但是更高硬度的新型材料使得加工更困难。通常使用PCBN作为切削材料,以获得合理刀具寿命。最佳的PcBN材料选择和合适的刃口处理是关键,刀片无振动稳定地安装在刀体上也是必不可少的。采用玛帕的气门座圈加工方案,刀片装在六方形刀片槽内,用以避免影响质量和刀具寿命的振动,即使是最细微的振动。六方形刀片槽作为一个刀片固定座非常精准地整合到刀体中,这样就无需对刀片做调整了。
由于气门导管承受着极大的载荷,所采用材料的稳定性与热传导性能扮演着至关重要的角色。在实践中,烧结金属越来越多地被使用,因为较其他材料,它们更便宜且耐磨性更高。然而因为耐磨性更高,对气门导管加工的铰刀要求也更高。玛帕有几个刀具方案可用,直径约6mm左右的导条刀具是首选。对于小直径,采用PCD整体刀头技术,就是用特殊焊接工艺把在整体PCD刀头焊接在硬质合金的刀体上。这种新型的生产工艺使刀具可以具有更多刀刃。在最近的一个应用案例中,直径为5mm的气门导管铰刀有6个以上的刀刃。
用这种刀具可以达到更好的圆柱度,更重要的是,刀具寿命比传统装备的刀具的增加了3倍。
购买铁艺配件、铁艺设备、铁艺材料,请联系无锡豪艺锦铁艺:www.hyjty.com,我是客服009,电话:13376206669
更多产品信息请关注铁艺大全网:www.tydq.net,转载请注明出处。