1、 总则
1.1、 本守则规定了钣金件、焊接件在下料、折弯、焊接、清理、焊接等主要工序的工艺守则。
1.2、 当本守则与工艺文件和图纸冲突时,以工艺文件和图纸为准。
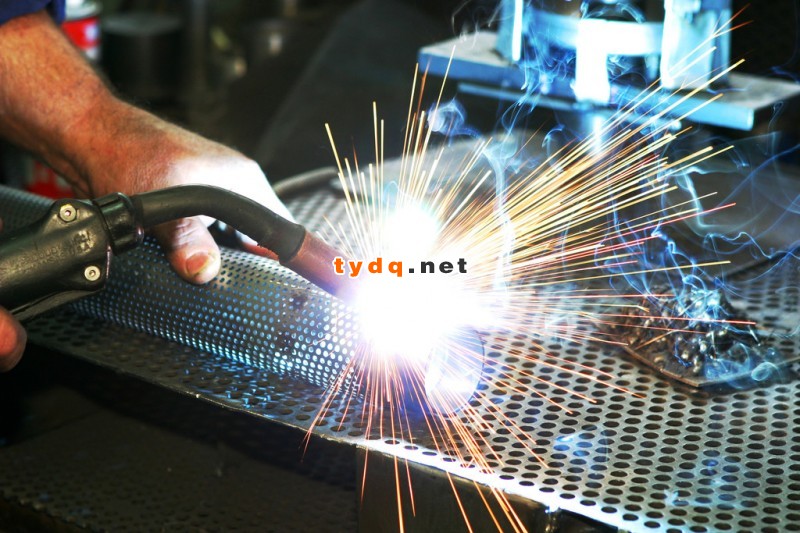
2、 零件的下料
2.1、材料的清理:
2.1.1、零件使用的板、型材原则上要求下料前进行抛喷丸清理后在进行切割。尤其是图纸尺寸小、下料后和焊接后难以进行抛丸清理的小件,更要在下料前进行清理。
2.1.2、振动类工件,必须使用原平板,或者依照图纸要求材质使用板材。所使用的板型材必须进行焊前清理。
2.2、钣金件的下料一般采用砂轮切割机下料、剪板机下料、冲床下料、手工气割下料、自动气割下料、等离子切割下料等方式,具体下料方式一般按以下原则进行选择:
a、图样及工艺文件已明确规定的应按照图样及工艺规定的执行。
b、适用剪板机下料的必须用剪板机下料。
c、型钢下料应尽量采用切割机下料。
d、适用自动气割机下料的应尽量采用自动气割机下料。
e、图样要求下料表面粗糙度Ra≤25的应采用剪板下料、自动气割机下料。
2.3、零件下料技术要求:
2.3.1、下料尺寸应符合图样及工艺文件的要求。
2.3.2、下料后进行机械加工的零件应留有合理的加工余量。
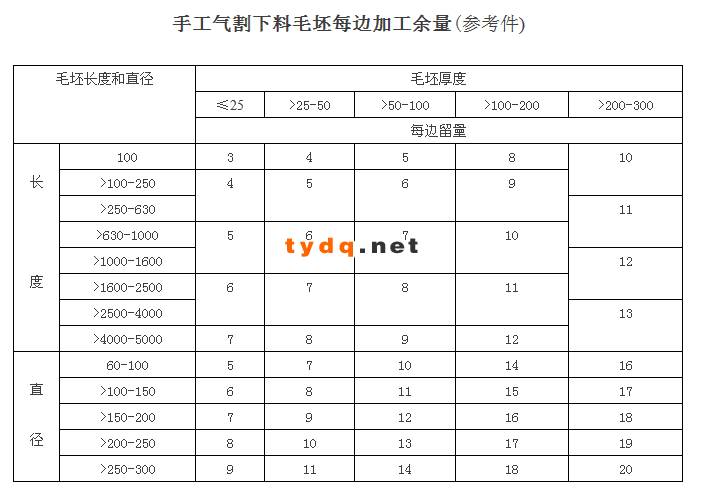
2.3.3、剪板下料的工件周边应齐平,不得有咬边现象,直线度误差每1000mm≤1.5mm,相互垂直面的垂直度每1000mm≤3mm。
2.3.4、气割下料前应检查场地是否符合安全要求,工件应垫平,工件下面应留有一定间隙,为防止飞溅物烫伤,必要时应加挡板遮挡。
2.3.5、气割切口表面应光滑干净,而且粗细纹要一致,边缘棱角无融化,直线表面直线度误差每1000mm≤3mm,相互垂直面的垂直度每1000mm≤5mm。
2.3.6、下料后直接入半成品库的零件应采用锉削、磨光机打磨。钢丝刷刷除、喷砂校直等措施保护零件的表面质量。
2.3.7、下料后直接入半成品库的零件应表面平整,无毛刺、锈蚀、气割飞溅物、明显弯曲及凹凸不平等现象,并按《涂漆工艺守则》的要求涂底漆。
3、 零件的弯曲
3.1、零件的弯曲一般采用折弯机折弯、冲床模具弯曲、卷板机弯曲及手工火焰加热弯曲等方法。具体选择方式按下列方式选择:
a、图样及工艺文件已明确规定的应按图样及工艺规定的执行。
b、材料较薄、尺寸较小等零件应尽量采用折弯机折弯、冲床模具下料等工艺方法。
3.2、弯曲件的技术要求:
3.2.1、直接入半成品库的零件按2.3.6的要求进行表面清理。
3.2.2、零件表面应平整、无毛刺、锈蚀及明显的凹凸不平等现象,并按《涂漆工艺守则》的要求涂底漆。
3.2.3、零件尺寸应符合图样要求、未注尺寸公差符合IT14级的要求。
4、 零部件的焊接
4.1、焊接前对各零部件依照图样进行认真检查,如发现材料尺寸不符合或有严重缺陷的不得进行焊;机械加工件不得有磕碰划伤现象,影响外观质量的不得擅自使用;以上情况应及时上报质检员,并由质检员重新确认是否可以使用。
4.2、电焊条、焊丝等质量必须符合国家有关标准的规定。
4.3、凡标牌不清、品质不明、包装破损或储存期过长的焊条、焊丝,必须经检验鉴定符合标准规定后方可使用。
4.4、电焊条受潮及存放时间较长应进行烘干后方可使用。
4.5、焊接前应检查周围环境、焊接设备及工具是否符合工艺和安全要求。
4.6、电焊条、焊丝的选用应根据以下原则选择:
a、当焊件母材为低碳或低合金钢时应按强度等级原则选择。
b、对于耐热钢、不锈钢等应选择与母材化学成分一致的焊条。
c、根据焊件的工作条件、使用性能及焊接设备、工艺条件、焊接效率和经济性选择。
d、图样及工艺有要求的按图样、工艺规定的执行。
4.7、焊接设备的选择应根据零部件的材料、结构、设备工作场地进行选择,图样及工艺有要求的按图样、工艺规定的执行。
4.8、零件的焊前清理:
4.8.1、焊接前应清除锈蚀、氧化皮、油污、气割飞溅物等,焊件有明显弯曲和凹凸不平的应校直校平后再进行焊接。
4.8.2、机械加工件焊前必须清理锈蚀和油污,清理过程中注意保护加工件的外露边或面,尤其是焊后不加工的光面。
4.8.3、焊接后无法进行除锈、清除氧化皮等表面处理的应进行表面处理后再进行焊接。
4.9、焊接过程的工艺要求:
4.9.1、为保证各焊接零件之间的相互位置应首先进行定位焊接,自检焊件位置尺寸无误后再进行连续焊接。
4.9.2、钢板之间、型材之间或者相互之间的对接,焊接接头对口的错边量不得超出下表的规定:
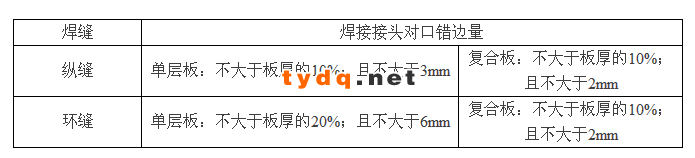
4.9.3、焊接较大构件时为减小焊接变形,应根据焊缝的不同部位、变形的方向采用合理的焊接顺序和焊接方向,尽量采用对称焊接法进行焊接,对变形量较大的构件应先进行小部件组焊,组后将各组焊件拼焊成形。
4.9.4板材拼接时应根据板厚预留0.5mm—3mm的间隙。
4.9.5、根据焊件的材质、厚度及焊接设备、焊接部位、焊条及焊丝规格等选择合适的电流、电压、焊接速度及运条方法。
a、多层多道的CO2气保焊尽量采用小焊脚,保证焊缝均匀平滑。角焊单层焊脚一般不大于6mm最大不能超过10mm,如:12—15mm焊脚需要采用两层四道焊缝。大焊脚的长焊缝尽量根据位置采用埋弧焊。
b、“V”型坡口CO2气保焊,单层焊缝厚度不大于6mm,打底焊不大于4mm。
c、平焊缝单道焊缝宽度不大于8mm,焊缝高度不高于3mm,直线度和平面度≤2mm。
d、CO2气体保护焊电流须在260A以上才能获得较大熔深。在开坡口(钝边≤2
且留间隙)条件下,使用Ф1.2的焊丝打底焊推荐电流90—120A。填充焊和盖面焊可适当加大电流,确保层间融合并避免冷裂纹。
4.9.6、焊接铸铁件等较重要件时应先坡口、预热后再焊接,并采取保温措施。
4.9.7、焊缝多层施焊时,应将前道焊缝的焊渣清理干净,并打磨焊瘤将不良焊缝修磨至合格。 4.9.8、焊缝的补焊应先清除油污、重新坡口、打磨后再进行焊接。
4.10、零件的焊后检查及返修:
4.10.1焊缝表面及热影响区不允许有裂纹。
4.10.2焊缝咬边深度不得大于0.5mm,咬边连续长度不得大于100mm,每条焊缝咬边总长度(焊缝两侧之和)不得超过该焊缝长度的10%。
4.10.3应尽量避免机械损伤,如有机械损伤其深度不应超过板厚的5%,且不大于2mm,如缺陷超出上述规定时进行修补。
4.10.4. 试压时发现焊缝渗漏应及时进行修补,但决不允许采取表面覆盖的施焊方法,因裂缝返修时必须经检验,技术部门组织进行质量分析,找出原因后进行。同一部位的返修次数一般不得超过两次。
4.10.5凡需焊后热处理(退火、淬火、发蓝等)之产品的焊缝必须在热处理前返修好。
4.10.6焊缝的修补,应采用产品同种焊接材料。补焊前预热温度应比产品焊前预热温度高5℃。
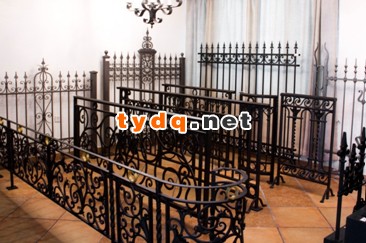
5、焊接件的质量要求:
5.1、焊接件的坡口及各构件相互位置、尺寸、焊缝尺寸及焊接强度必须符合图样及工艺的要求。原则上6mm以上板需要坡口,8mm以上板需要多层多道。
a、破口面不应有重皮裂纹,应除掉油污及锈蚀物。
b、对等离子切割的坡口表面应打磨光滑至露出金属光泽。
c、自动焊的坡口两侧20mm范围内必须打磨光滑至露出金属光泽。
d、手工坡口应使用角铁等简易工装作为依托,以确保坡口宽度深度一致,并去除氧化皮。
5.2、对于焊接后进行机械加工的焊件必须依据图样规定、工艺要求及加工面的面积、变形大小、加工精度选择合理的加工余量。
5.3、焊接应牢固可靠,焊缝应均匀、圆滑、美观,不得有明显的裂纹、气孔、夹渣、未焊透、咬边、漏焊、虚焊、烧穿等缺陷,接头处和收弧处不得有凹坑。。
a、各零部件的焊接成型应符合图纸的要求,不允许在受力部位或外观表面上改变焊接型式。
b、焊接表面不允许出现裂纹、假焊、气孔、焊渣、咬边、焊穿及明显的焊缝凹凸不平等焊接缺陷。
c、焊接时的焊缝严格按图纸要求,该连续焊的连续焊,该断续焊的一定要断续焊(如图纸没有要求的断续焊,钢板厚度≤4mm,每间隔200mm焊50mm;钢板厚度>4mm,每间隔150mm,焊50mm)。型钢立柱类每间隔200mm焊50mm,螺旋轴两面采用断续焊,每间隔 150mm,焊50mm。
5.4、图样规定进行压力试验、致密性试验的应按照规定进行压力试验和致密性试验,并符合图样及工艺要求。
5.5、焊接后应进行打磨、抛丸等清理,清除焊渣、毛刺、锈蚀、氧化皮、飞溅物等。
5.6、焊接后变形比较大的应进行校直校平。
5.7、焊接后应自检焊件尺寸、构件位置是否符合图样要求。
5.8、焊接后的零部件在吊装和周转时,应确定合理的吊装位置和存放方法,保证焊件不得发生永久变形。
5.9、图样工艺有消除应力要求的必须进行退火或振动时效处理,所有的补焊作业必须在退火或时效前完成。
5.10、焊接后无法涂底漆的部位应先涂漆后焊接。
5.11、焊接件的清理和涂漆应符合《涂漆工艺守则》的要求。
更多产品信息请关注铁艺大全网:www.tydq.net,转载请注明出处。