1.平面磨床主要改造简介
机床原有垂直进给、前后进给是由手摇进给和快速电动进给两部分组成,通过T牙丝杆副、滚珠框导轨、蜗轮蜗杆副、交换齿轮、交流电动机和手轮实现的。其结构非常繁琐,数控化改造后,手摇机构去除,将T牙丝杆副改换成我公司生产的滚珠丝杆副,将原有的快速进给交流电动机更换成交流伺服电动机, 并重新制作了与电动机匹配的蜗轮蜗杆箱,实现垂直进给、定位和自锁,手动进给可以通过数控系统手脉进行,通过打表测量, 目前两轴的定位精度和重复定位精度都分别不大于0.006mm和0.005mm。
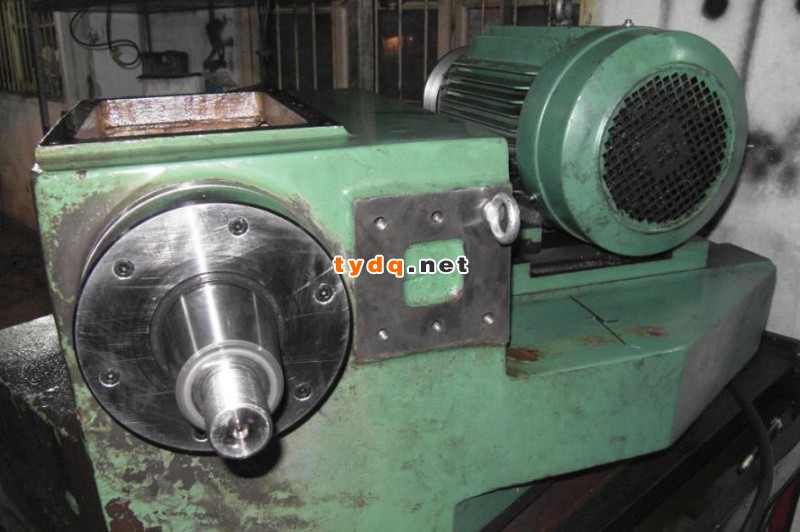
2. 原有液压系统工作台运动描述及参数
原有液压系统是老式平面磨床标配的液压系统, 多年前PLC技术或者是数控技术发展的不是很成熟,这样的系统采用的是液动模式,特别是工作台往复运动,换向很不稳定,冲击力大。配置了一台功率为4kW、转速为2 900r/min、流量为90L/min 的螺杆泵, 螺杆泵将油从油箱里抽出,经过网式滤油器2,通过溢流阀18调整其压力(1.2~ 1.5MPa)后进入开停调速阀17、换向阀7再进入到液压缸的左右腔, 带着工作台左右运动, 如图1所示。油管内径为42mm, 液压缸直径为63mm,活塞杆直径为35mm,液压缸的有效面积为:(31.5×31.5-17.5×17.5) ×3.14=2 154mm2,整个液压缸长度为2 200mm, 理论最大速
度V=Q/S=90 000/(31.5×31.5- 17.5×17.5)×3.14=4 180cm/min =41.8m/min。设备的正常工作速度在20m/min,应该说原有配置是比较富裕的。
3. 改造后的液压系统功能及参数
电液技术的加速融合。微电子技术的飞速发展,为液压技术的进步注入了新活力,液压器件是机电一体化的重要接口器件, 我们将其液压系统改为目前广泛使用的外置电液换向结构及电液比例调速方式。液压系统除液压缸与活塞杆之外, 其余全部更换,满足了平面磨床精磨时工作台运动换向轻松、平稳性好、精度高和可靠性好的要求。
电液换向电液阀(见图2) 由一只二通常开电磁阀、一只二通常闭电磁阀等组合而成,在管道输送介质过程中,当需要开启阀门时, 由计算机发出阀门开启信号, 常开电磁阀通电( 关闭),同时常闭电磁阀通电(开启)。这时,由上游通向主阀膜片上的腔室通道被截止,主阀膜片上腔室通向下游的通道被导通。此时,膜片下部的压力高于上部压力,主阀膜片上的腔室的介质通过常闭电磁阀通道排向下游管道,主阀被打开。压力油通过主阀进入液压缸,反之亦然。
电液比例阀调速阀( 见图3):当液压油从P1口调速阀后, 经过定差减压阀1(压力预先设定后)进入节流调节阀腔2,如果比例电磁铁流量控制电磁线圈没有输入电流,则节流阀芯轴因弹力而关闭,所以出口P2并没有液压油流出,液压无法动作,若流量控制电磁线圈有输入电流(电流的大小由PLC输出信号,经过放大板放大后作用到线圈上)时就会产生向左的推力而将节流调节阀轴打开一个开度,出口L即会出油,此节流阀轴的开度会依据输入电流的大小而产生变化,输入电流越大则产生的推力越大, 此开度会变大,这表示可通过的流量越多,所以可依据输入电流的大小来调整通过流量的多少进而控制作动器的速度快慢。有的电液比例阀调速阀对压力也有一定的控制,设计时也可以电控, 调速线性好,精确度高。比例阀的发展主要在频宽的增大及控制精度的提高上,以期性能接近伺服阀。同时,比例阀又沿着标准化、模块化及廉价的方向发展, 以促进其应用。
工作台的快进运动速度拟定为22m/min(完全能够达到工艺要求),设备的工作压力仍在压力(1.2~1.5MPa),根据这要求选定液压泵的流量。
快进阶段的液压缸流量: q=A·v k=2 154×25/1 000=47.38 L/min,进行估算。由于系统流量较小,故取泄露系数K=1.3,则液压泵供油流量约62L/min。
确定液压泵: 液压泵是液压系统的动力元件,靠电动机驱动,从液压油箱中吸入油液,形成压力油排出,送到执行元件的一种元件,液压泵的大小、选择合理与否直接影响到整个液压系统的压力、流量和速度。液压泵目前在机床上用得多的为齿轮泵、柱塞泵和叶片泵。齿轮泵体积较小,结构较简单,对油的清洁度要求不严,价格较便宜;但泵轴受不平衡力,磨损严重,泄漏较大;柱塞泵容积效率高、泄漏小、可在高压下工作、大多用于大功率液压系统但结构复杂, 材料和加工精度要求高、价格贵、对油的清洁度要求高;叶片泵分为双作用叶片泵和单作用叶片泵,这种泵流量均匀、运转平稳、噪声小、工作压力和容积效率比齿轮泵高、结构比齿轮泵复杂。这次我们根据压力、速度综合考虑,选着了叶片泵。
拟初选液压泵的转速为n1=1 000r/m i n,泵的容积效率ηv=0.8,则可算得泵的流量参考值为
Vg=1 000qv/(n1·ηv)=77.5 L/min
根据以上计算结果查阅产品样本, 选用规格相近的叶片泵YB1-1980,泵的额定压力为6.3MPa,流量为80L/min,液压泵电动机的选择——最大功率出现在快退阶段,已知泵的总效率为ηp=0.8,则泵的快退所需的驱动功率为:Pp= Vg×30(最高压力)/600×0.8=5kW,所以电动机选5kW,三相异步6级电动机。
4. 改造后液压系统原理图(见图4)及描述
机床PLC发出指令,液压泵电动机启动, 压力油经过滤油器、叶片泵进入主管道,双位电磁溢流阀用来控制油路的主压力和卸荷。机床不工作时,处于中位,液压泵零负荷启动,电磁溢流阀的两个电磁铁分别和电液换向阀的电磁铁同步得电,电压为DC24V,当系统PLC指令DT0 得电时,电磁换向阀DT4同时得电,压力油经过单向阀CIT-10、精密滤油器、进入电液比例调速阀后,由机床PLC发出的0~10V 的控制电压作用于电液比例调速阀的线圈,以此控制经过电液比例阀的压力油流量,压力油从比例阀出来后分两路进入换向阀和以控制油路形式控制油路中的电磁换向阀,由于此时电磁换向阀DT4得电,控制液压油经过A口进入换向阀的左端,使得主压力油从P口流入到换向阀的A口, 进入液压缸的左端,使得工作台左移,液压缸右端的回油从换向阀的B口流入到T口,经过背压阀HCG-06回到油箱,反之原理一样。当设备磨削完工件后,工作台需要停止时,此时双位电磁溢流阀7的两线圈全部失电,压力油直接回到油箱,整个液压系统处于卸荷状态,比例阀回到初始位置。
5.调试及使用过程中注意事项
比例调速阀使用了进油节流形式,需依靠背压阀消除液压缸寸动, 背压阀在调试时找到压力调定点,根据附表进行调节,原则上越低越好。
起步调试时,将电液比例阀的线圈脱离,手动调节电液比例阀顶端的调速旋钮,将工作台运动调至最低位时(临界点),将线圈插上,此工作点则设为比例调速的最低速;经常清洗两过滤器,防止影响油液压系统中的流量和压力油的清洁度。
6. 结语
改造后效果设备自动化程度较高故障率低,由电液换向和电液比例调节组合而成。不漏油,调速更加平稳,换向可靠性好、易维护,提高了设备工作性能。液压系统的改造费用约1.5万元,整个设备的数控化改造费用不足5万元(含数控系统费用),改造性价比还是不错的。
更多产品信息请关注铁艺大全网:www.tydq.net,转载请注明出处。