目前,在工农业生产以及日常生活用品中,钢铁制品仍占有绝对的份额。以钢铁为原材料,制成各种零部件以后,必须对零部件的表面进行适当的处理,否则,其表面裸露在大气中,与空气中的氧气发生化学反应后,会很快出现腐蚀现象,使零部件逐渐失去其原有功能,最后使整个设备或产品无法使用,造成资源浪费。表面处理技术,包含表面覆盖技术、表面改性技术及复合表面处理技术3部分。而在这3部分中,应用最广泛的是表面覆盖技术,在该技术中应用最多的是涂装工艺,因为该工艺具有质优价廉的显著特点,在满足零部件防腐功能的同时,还具有良好的装饰作用。传统的涂装工艺仅指喷漆工艺,随着科学技术的不断进步,从20世纪80年代起,喷塑工艺作为后起之秀,在我国逐渐进入了涂装领域,且在某些应用领域大有取代喷漆工艺之势。因此,现在我们所指的涂装工艺,包含喷漆工艺和喷塑工艺两部分。本文就这两种涂装工艺的特点,做一简要概述。
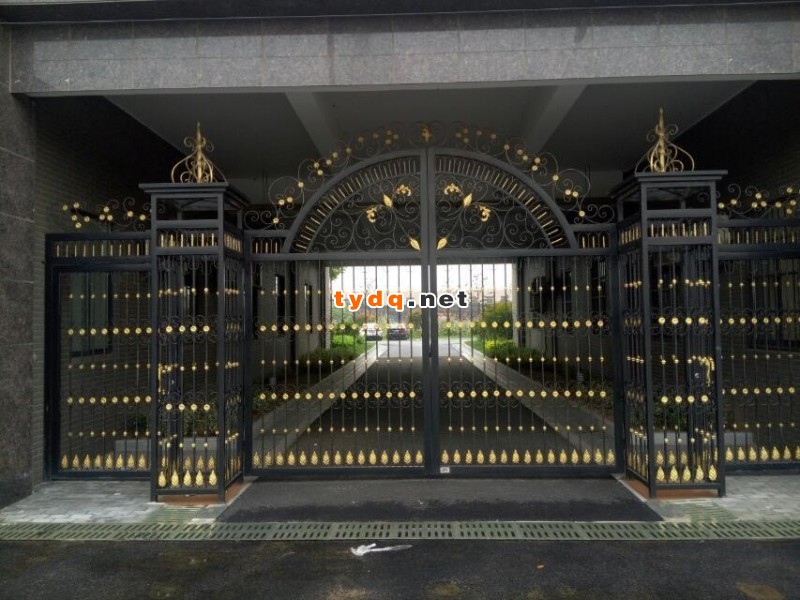
1喷塑工艺与喷漆工艺各自的特点
1.1喷塑工艺
1.1.1无溶剂、减少公害
油漆在生产、运输、贮存以及施工过程中,由于溶剂的挥发会给大气或水造成严重污染,并给操作人员带来身体伤害。如果保管和操作不当很容易引起火灾,此外废漆处理也十分困难。而粉末涂料不含任何溶剂,是100%固体分的涂料,它的制造、运输、贮存和施工解决了因溶剂而造成的污染问题,改善了操作人员的劳动条件,有利于操作人员的身体健康。
1.1.2简化涂装工艺,提高涂装效率
在采用油漆工艺涂装时,需经喷涂底漆、刮腻子、水磨、喷面漆、喷罩光漆等“三磨三抄”十多道至二十多道工序,七至十天加工周期。而采用喷塑工艺涂装只需喷涂、固化、冷却等3道工序,一次成膜。大大简化了涂装工序,缩短了生产周期,当天就能出产品。在粉末涂料静电涂装中,配置自动涂装机械和回收循环系统,就能形成自动化生产,从而节省了能源和资源,提高了生产效率。
1.1.3粉末涂料利用率高,并可回收再用
与油漆相比,粉末涂料可以直接涂覆至被涂物表面,经烘烤固化后形成涂膜,而且未被涂上的粉末回收后可再送入供粉系统中使用,从而大大减少了涂料在施工中的损失,粉末涂料的利用率约在95%以上,而油漆除溶剂全部挥发损失外,未被涂上的油漆很难回收再用,故一般油漆的实际利用率在50%左右。
1.1.4粉末涂膜性能好、坚固耐用
粉末涂料可以利用常温不溶于溶剂的树脂,或不易溶解而无法液体化的高分子树脂来制备具有各种功能的高性能涂膜。且粉末涂料在制备或成膜时,没有溶剂加入和释放,不会产生贯通涂膜的针孔,因此涂膜更致密。与油漆涂膜相比,粉末涂膜更加坚固耐用。
1.1.5可实现一次性涂装
粉末涂料一次涂装就能得到50~300μm厚的涂膜,并且不易产生油漆厚涂时的滴垂或积滞,不发生溶剂针孔,不造成厚膜涂装的缺陷,而且边角覆盖率也很高。而油漆一般一次涂装的膜厚在5~20μm,如果要得到厚涂膜或中高档要求的涂膜,必须经过多次涂装方可实现。
1.1.6调色换色困难,周期较长
由于粉末涂料调色不可能像油漆那样可以用原色料现场调配,粉末涂料的颜色在出厂时已经确定,如果要改变其颜色,就需要改变粉末涂料的配方,所以很难在短时间内完成调色工作。粉末涂料的换色也比较麻烦,由于采用静电喷涂,如果作业过程中间换色,就必须将喷枪、供粉器、喷粉室、输粉管、回收系统等全部清理干净,否则将严重影响涂膜表面质量。特别是深色与浅色的变换更为复杂,故不易在短时间内变换多种色调。
1.1.7不易实现涂层薄膜化
由静电喷塑的工艺原理所致,粉末涂料的膜厚一般均在50μm以上,即使粉末涂料精良,施工条件良好,最低的膜厚也在40μm左右,要形成40μm以下的涂膜目前十分困难。
1.1.8涂膜的外观平整度略差
由于粉末涂料是借助于加热熔融而流平在被涂物上的,所以其熔融粘度高,易呈轻微桔皮状,涂膜平整度不如油漆。
1.1.9具有一定的局限性
喷塑工艺的局限性主要表现在3个方面:首先由于粉末涂料固化温度一般均在160℃以上,这就限制了其在一些不耐热的产品(如塑料)上的应用;其次由于喷塑工艺绝大多数采用静电喷涂,因此被涂物必须能导电,这就要求被涂物须是金属件,如果是非金属件则表面必须经过导电处理,并且能耐160℃以上的温度;最后,在实际工作中,基于经济性考虑,喷粉室、烘干室以及前处理槽不可能做得很大,因此大型工件(如列车车厢、桥梁、塔吊等)均不能采用喷塑工艺。
1.2喷漆工艺
1.2.1油漆品种繁多,选择范围广
采用油漆工艺涂装产品已有数千年的历史,工艺成熟,油漆品种繁多,根据成膜物质我国将油漆分为十七大类,生产的各种油漆已多达上千种,新的品种还在不断涌现,既有用于航空、航天等高科技产品上的专用油漆,又有用于舰船的甲板漆、水线漆,还有家庭装修常用的乳胶漆,可谓琳琅满目,门类齐全。用户可以根据产品的性能、用途、使用环境等因素,有针对性地选择油漆,以期达到相对最佳的涂装效果。而粉末涂料目前只是简单地分为室内用和室外用两类。
1.2.2工艺手段齐全,适应性强
油漆作为一种有着悠久历史的传统工艺,并随着科学的发展,其工艺手段更加趋于完善。目前油漆涂装的方法有刷涂法、浸涂法、淋涂法、辊涂法、刮涂法、空气喷涂法、高压无气喷涂法、电泳涂装法、静电喷涂法等,其中刷涂法、空气喷涂法和电泳涂装法应用较为广泛,一般的厂家绝大部分都采用空气喷涂法和刷涂法,当产品大规模生产且对涂膜表面质量有较高要求时,如轿车表面的涂装,则可采用电泳涂装法。
1.2.3设备一次性投资少
如前所述,空气喷涂法是目前涂装厂家使用最广的施工方法,适宜于中、小涂装作业。操作是手工的,喷涂质量的好坏取决于操作者的熟练程度,但生产效率远高于刷涂法。具有施工简单,涂膜均匀、平整光滑等特点。所需设备仅有喷枪、空气压缩机、油水分离器及必要的输气胶管等附件,与喷塑工艺动辄几十万、上百万的设备投资相比,设备一次性投资少,生产成本低,资金回收快。至于常用的刷涂法,是一种最原始和最简单的涂装方法,用漆刷蘸漆后在被涂物上涂展。具有工具简单、操作不受场地所限、被涂物不拘形状和大小等特点,除了干燥快和涂展性不良的挥发性油漆外,任何油漆都可采用刷涂法施工。在采用刷涂法涂装工件时,仅需刷子、拂尘刷、腻子刮刀、砂纸、搅拌用不锈钢或木质搅棒、棉纱和细铜丝网等工具和材料,其成本与喷塑工艺相比,简直可以忽略不计。
1.2.4可以简化前处理工序
由于喷塑工艺通常采用静电吸附方式将粉末涂料直接喷涂到裸露的金属表面,因此对被涂物的前处理工序要求较为严格,在喷塑前必须确保被涂物无油、无锈、无任何杂质,且被涂物表面应有一层均匀分布的磷化膜,用以提高涂膜的附着力和耐腐蚀能力;否__则会影响涂膜质量,在不太长的时间内,涂膜就会出现锈迹、脱落等缺陷,严重影响涂膜的使用寿命。而在采用喷漆工艺时,由于底漆具有优良的防锈性能,与基材和面漆的附着力良好,故极大地提高了涂膜的耐腐蚀性能,能确保涂膜的使用寿命。只需对被涂物进行除油和除锈处理,而不需经过磷化处理,即可对被涂物喷涂底漆。因此简化了前处理工序,节约了生产成本,提高了生产效率。
1.2.5对操作者的技能要求较高
由于油漆的品种繁多,这就要求操作者对各类油漆的用途、性能、使用范围、施工方法、操作中的注意事项以及各类油漆的配套性都要做详细地了解,并需具有一定的色彩学知识,能根据需要,利用原色调配出被涂物所需的色彩。一般油漆涂膜由底漆、腻子、面漆3部分组成,因此在施工时须掌握正确的涂装工艺,避免出现涂膜质量问题。同时在采用常用的空气喷涂法或刷涂法时,由于二者均为手工操作,其涂装质量与操作者的技术水平密切相关。一名合格的喷漆操作者,不但应具有相关的理论知识,还应具有娴熟的操作技能。
1.2.6生产周期较长,综合成本高
喷漆的工序多于喷塑工序。一般来说,典型的喷漆工艺包含以下6个步骤:首先是涂装施工前的准备工作,具体内容为:涂料性能检查、充分搅匀涂料、调整涂料粘度、涂料净化过滤、涂料颜色调整;其次是涂底漆;第3步是涂刮腻子;第4步是涂中间涂层;第5步是打磨;最后一步是涂面漆。在施工过程中,要使用底漆、腻子、稀释剂、面漆等多种材料,各个工序之间须留有干燥时间,有些油漆不能自然干燥,还需进行加热烘干。因此,无论从材料消耗、能源消耗,还是人工成本诸方面来讲,喷漆工艺的综合成本均高于喷塑工艺,且生产周期较长。
1.2.7环保性差,有损操作者身体健康
由于油漆含有一定的有机溶剂,在施工和固化过程中,这些有机溶剂易挥发到空气中,在采用空气喷涂法时,还会产生大量的过喷漆雾。上述两个原因产生的废气,如果不经处理直接排入大气,将会对空气、生物及环境造成极大的污染和危害。有机溶剂的毒性很大,吸入体内,将危害人的呼吸器官、神经系统和造血系统。涂装生产过程中产生的大量漆雾微粒是湿性粉尘,它包含涂料的全部组成,如颜料、树脂、各种辅助材料及有机溶剂等。这些化学物质进入人体会危害呼吸道、肺、胃及其它器官,还能引起铅中毒。有机溶剂和涂料微粒还会损害皮肤,又可通过皮肤进入体内,造成危害。
1.2.8火灾危险性高于喷塑工艺
我们说采用喷漆工艺的火灾危险性高于喷塑工艺,基于如下3个理由:首先是由于油漆中含有易挥发的有机溶剂,在施工及涂膜固化过程中,溢出的有机溶剂在空气中积聚到一定的浓度,一旦接触明火(火花、火星),就很容易引起燃烧和爆炸,而粉末涂料的成分中不含有机溶剂,故危险性低于喷漆工艺;其次是油漆的燃点、闪点、点火能量均低于粉末涂料,燃烧扩散速度快于粉末涂料,因此在相同的条件下,喷漆工艺的燃烧和爆炸危险性高于喷塑工艺;最后,在采用常用的空气喷涂法涂装工件时,无论是通风设备、还是施工环境以及操作规程均逊色于喷塑工艺,因此前者发生火灾的危险性要高于后者。有一点须特别指出,尽管喷漆工艺的火灾危险性高于喷塑工艺,但是一旦粉末涂料发生爆炸,其爆炸的强度和破坏力将远大于液体涂料。
2结语
就目前的涂装技术而言,喷塑工艺和喷漆工艺各有千秋,二者之间具有互补性,而不是替代关系,因此在选择涂装工艺时,应具体情况具体分析,扬长避短,从技术可行性和经济合理性两方面进行分析,从中选择出切合实际的、相对最佳的涂装工艺。只有这样才能在确保获得优异涂膜质量的同时,降低涂装成本,为企业创造出更多、更好的经济效益和社会效益。
更多产品信息请关注铁艺大全网:www.tydq.net,转载请注明出处。